Breadcrumb
Anti-block: Masterbatch vs. liquid - what is more economical in PET sheet production?
Blocking is the effect when calendered PET sheet can no longer be separated from each other after winding. A common method to prevent this from happening is to add masterbatch to the extrusion process. An alternative is the application of anti-block liquid to the surface of the sheet. To find out which method is more economical under which conditions, SML has made some investigations.
“The blocking of sheet generates difficulties. Unwinding might become troublesome or even impossible, thermoformed cups and trays can no longer be unstacked. As measures to avoid blocking contribute quite significantly to the overall production costs of the sheet, we have compared the costs of masterbatch to the costs of anti-block liquid,” Martin Kastner states.
Calculating the costs for masterbatch
To calculate the cost of masterbatch, it is important to differentiate between coextruded and mono sheets. Whereas in co-extruded sheet - with a coex layer structure A/B/A - the masterbatch is only added to the outer layers (A layers), in sheet with a mono-layer structure the quantity of masterbatch is determined on the basis of the total sheet mass. Thus, the formulas for calculating the costs for masterbatch are as follows:
Coex-layer structure A/B/A
€Masterbatch = mA‒layer x iMB x €MB
Mono-layer structure
€Masterbatch = ms x iMB x €MB
€Masterbatch: costs for masterbatch [EUR]
mA‒layer: mass of A-layer in coex-layer structure [kg]
ms: mass of sheet in mono-layer structure [kg]
iMB: percentage of dosed masterbatch [%]
€MB: costs for masterbatch [EUR/kg]
Calculating the costs for anti-block liquid
The costs for two-sided anti-block liquid (AB liquid) application are calculated by multiplying the total surface area of the sheet by the price per unit area of AB liquid. As subsequent drying is necessary with this method, we have to add the energy costs for drying the sheet after application:
AB liquid both sided
€AB liquid = As x mAB liquid x ie x €e + Ed x €e
€AB liquid: costs for AB liquid [EUR]
As: sheet surface [m²]
mAB liquid: applied AB liquid [kg/m²]
ie: percentage of emulsion in AB liquid [%]
€e: costs for emulsion [EUR/kg]
ED: energy consumption drying unit [kWh]
€E: energy costs per kWh [EUR/kWh]
Cost analysis masterbatch vs. AB liquid
“In order to compare the two methods, we based our calculations on the production of 1,000 kg of PET sheet with a film width of 1,250 mm and a line throughput of 1,000 kg/h with several sheet thicknesses,” Martin Kastner says. The calculations for the cost of masterbatch were made on a dosing quantity of 1.5 % and an average masterbatch-price of 4.8 EUR/kg.
For an equal outcome with AB liquid, this calculation is based on a 5 % emulsion with an application of 2 g/m² on both sides. Emulsion costs are calculated as 5 EUR/kg. The energy costs for the subsequent drying process were set at 0.15 EUR/kWh which were valid at SML at the time.
Masterbatch
“As our chart demonstrates, the amount of masterbatch required in co-extruded A/B/A film depends only on the mass of the A layers - and therefore on the layer distribution of the A/B/A layers,” Martin Kastner explains. The bigger the proportion of A layers, the bigger the mass of the A layers, and consequently the bigger the amount of masterbatch required. As the example in this chart shows: For a 10/80/10 film, the costs for 1,000 kg of PET sheet amount to EUR 14.4. If the proportion of A-layers is reduced by half (layer distribution 5/90/5), the costs are also halved to EUR 7.2. Changing the film thickness has no effect on the costs per kg of film.
“When producing monofilm (0/100/0) the 1.5 % of masterbatch, on which our calculation is based, must be used in relation to the total 1,000 kg film mass we have assumed. As we can see in the horizontal line on the top of the chart, the masterbatch costs of 72 EUR per 1,000 kg PET film are extraordinarily high,” Martin Kastner says.
AB liquid
In contrast to masterbatch, the amount of AB liquid required does not depend on the layer distribution of the film, but on the film thickness. The thicker the film, the smaller the film surface in relation to the mass of the film, and the lower the amount of AB liquid required. “Our example demonstrates that the pure costs for the emulsion are EUR 5 for a 150 µm thin film, and then fall as the film thickness increases. At 1,300 µm they are only EUR 0.6,” Kastner continues.
Then, the energy costs for the drying section are included in the calculation. With an assumed energy price of EUR 0.15/kWh, as is currently usual for Central Europe, energy costs represent a significant proportion of the total costs. As this chart shows, the costs for AB liquid including energy costs amount to EUR 12.2 for a 150 µm film. For a 1,300 µm film, the costs are EUR 7.8.
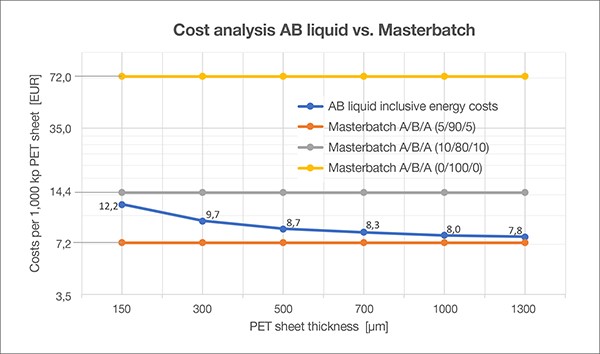
Comparing costs for masterbatch vs AB liquid – practical examples:
A comparison of the two methods for the production of 150 µm thin film shows that masterbatch at a layer distribution of 5/90/5 is the cheapest option, with EUR 7.2 per 1,000 kg of PET film. If the same film is produced with a layer distribution of 10/80/10, the costs for the masterbatch amount to EUR 14.4 and are therefore EUR 2.2 higher than when using AB liquid (EUR 12.2). If the film is produced as a monofilm, the masterbatch costs EUR 72, which is EUR 59.8 more than for AB liquid.
The thicker the film produced, the more the costs for AB liquid decrease, while the costs for the masterbatch remain constant. With a film with a thickness of 1,300 µm, AB liquid costs only EUR 7.8 for 1,000 kg of PET. Compared to masterbatch with a layer distribution of 10/80/10, this translates into potential savings of around 46 % (6.6 EUR).
Finally, comparing the costs on a yearly basis: When we take a 10/80/10 film with a thickness of 500 µm and an annual production of 10,000 tonnes manufactured under the conditions given above, the annual costs with AB liquid (including energy) amount to EUR 87.000. With the masterbatch on the other hand, the costs total EUR 144.000. Using AB liquid instead of masterbatch, helps to save EUR 57,000 per year!
“Depending on the sheet manufactured, the use of AB liquid can lead to significant cost advantages compared to masterbatch. We are happy to give our customers further insights into this topic and explain the specific advantages they can realise with our applicator unit”, Martin Kastner concludes.
Redlham, 20.11.2024