- Cast film lines
- Lines for CPP, CPE, CAST-PET, barrier and mono oriented-film
Lines for CPP, CPE, CAST-PET, barrier and mono oriented-film
Cast film products are primarily used in the packaging industry for food. However, as a result of their special qualities, they are also used in technical products, medical products and as a means of ensuring perfect surface protection. The films produced in this way make an impressive impact due to their low gauge tolerances, high transparency, suitability for metallisation and printability.
Our technology
The technology that was state-of-the-art yesterday may simply be run-of-the-mill tomorrow. That is why we at SML are always pushing the boundaries of what is possible. SML cast film lines are among the most adaptable in the world.
Line Types

Headline
Cast film production involves casting the melt on a chill roll. The films manufactured in this way are notable for their qualities such as low gauge tolerances, high transparency, suitability for metallisation and printability. The excellent cooling performance from direct contact with the chill roll allow for high production speeds and, in turn, high efficiency in the manufacturing process. In the casting process, films are produced in a gauge range of 12 to 350 µm, depending on the polymer and type of application.
We configure our machines to meet our customers’ requirements, with our strong team drawing on the extensive experience gained from installing hundreds of lines around the world.
Winding | winder W1050 | winder W1100 | winder W1200 | winder W2000 | winder W5000 |
---|---|---|---|---|---|
Winder | Turret | Turret | Turret | Hortizontal sliding | Linear turret |
Film thickness range | 15 - 100µm | 15 - 300µm | 15 - 100µm | 15 - 300µm | 15 - 100µm |
Max. mechanical diameter | 1,000mm | 1,000mm | 1,200mm | 1,000mm | 1,600mm |
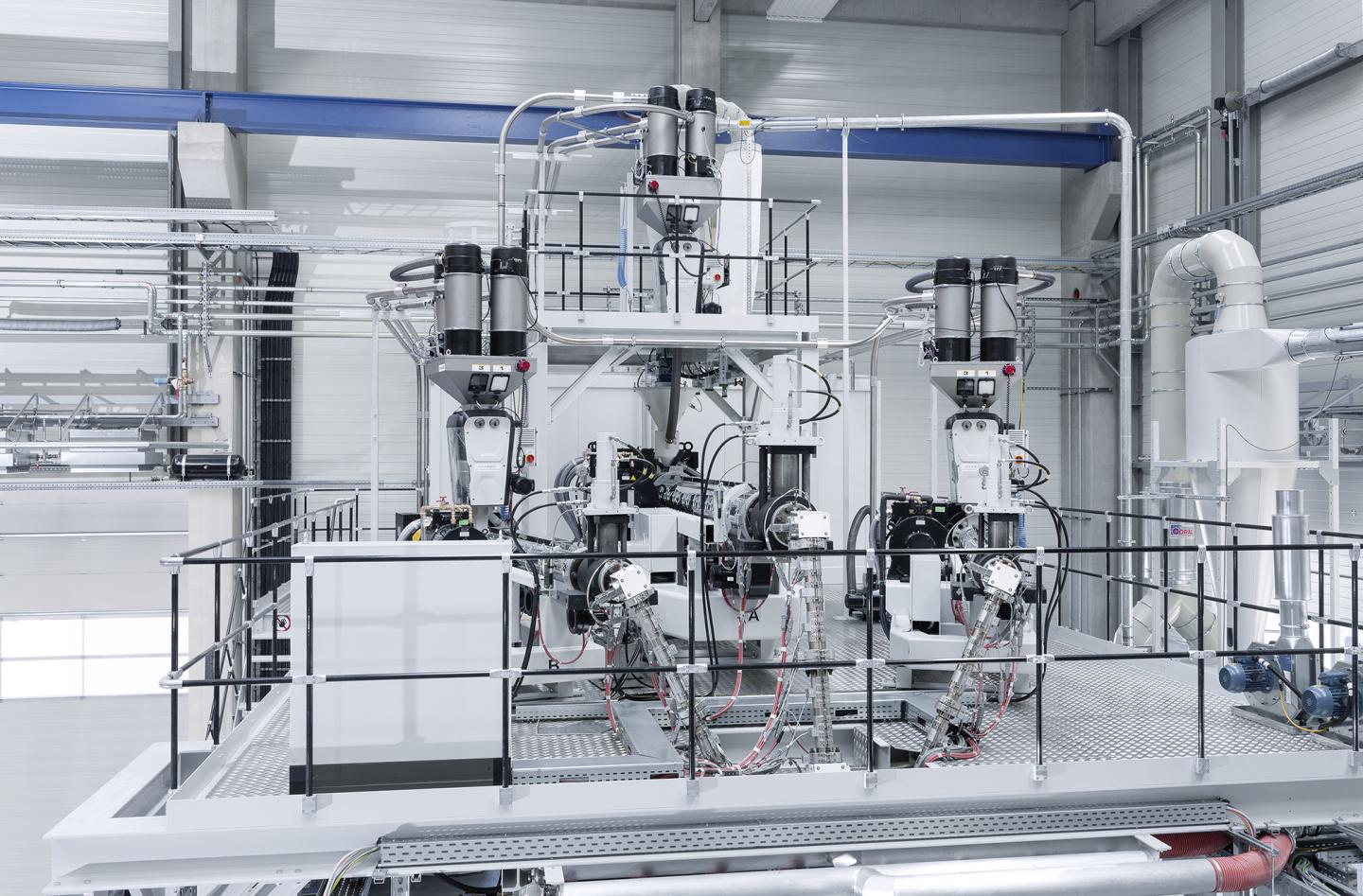
High-performance, energy-efficient extruders for all relevant polymers
SML extruders for cast films are designed in-house according to the processing requirements for the entire range of polymers used in this market segment.
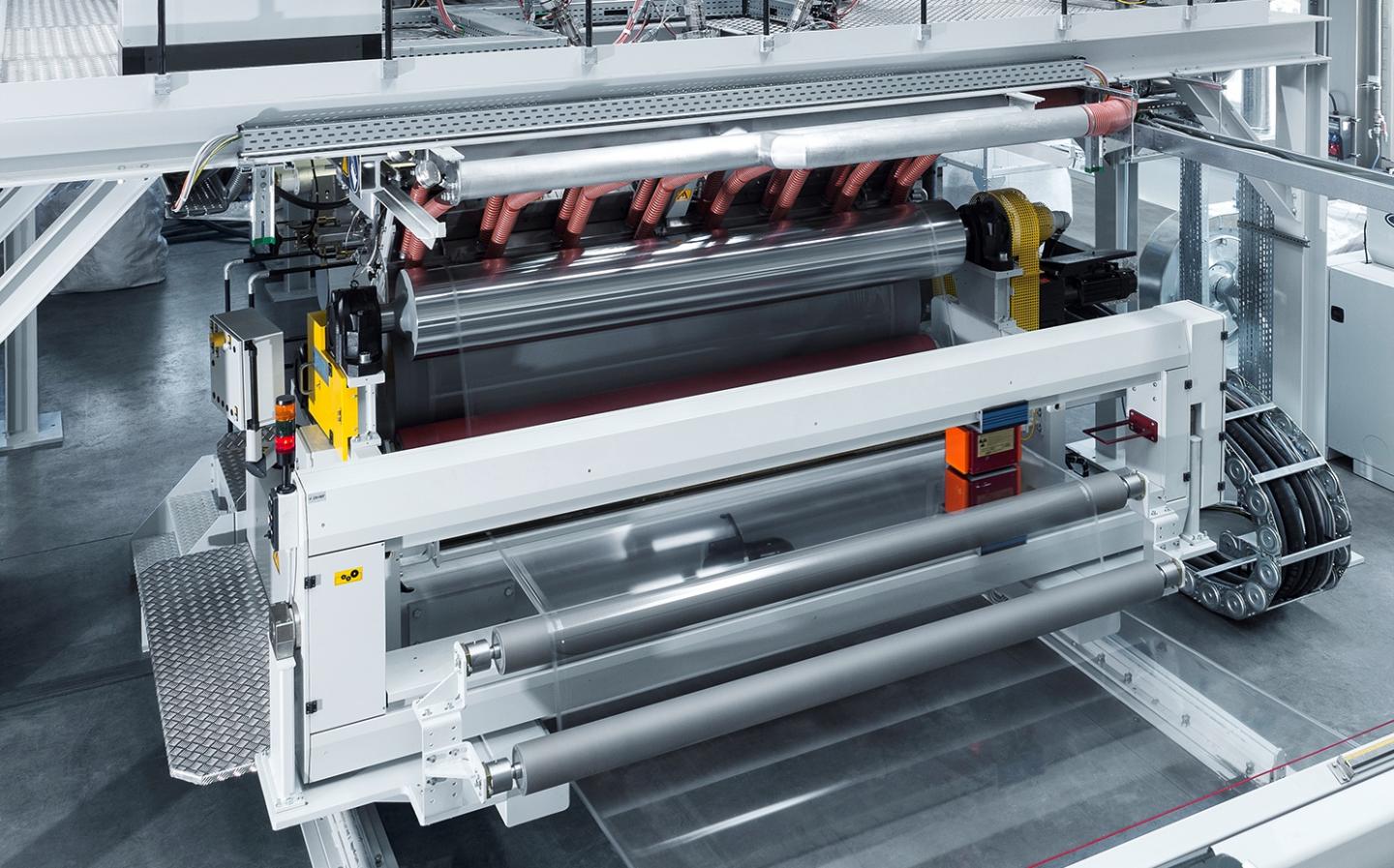
Casting section
In combination with the bi-vacuum box, air knife or soft box settings, the casting station has a significant influence upon final product quality factors such as haze, transparency, tensile strength, shrinkage, as well as possible production speeds.
All the chill rolls are equipped with separate water temperature control systems and accurate speed control drives. A cleaning roll prevents monomers and other deposits from contaminating the first chill roll.
Corona treater
Corona treatment is necessary in order to prepare films for subsequent offline printing, or the metallizing process. Depending upon customer requirements, one-sided reversible or double-sided treatment stations are employed.
What about waste?
Regranulating systems can be operated inline, allowing recipe-controlled refeed rates. Fluff refeeding is a very energy-efficient and material compatible method for the refeeding of bleed trims.
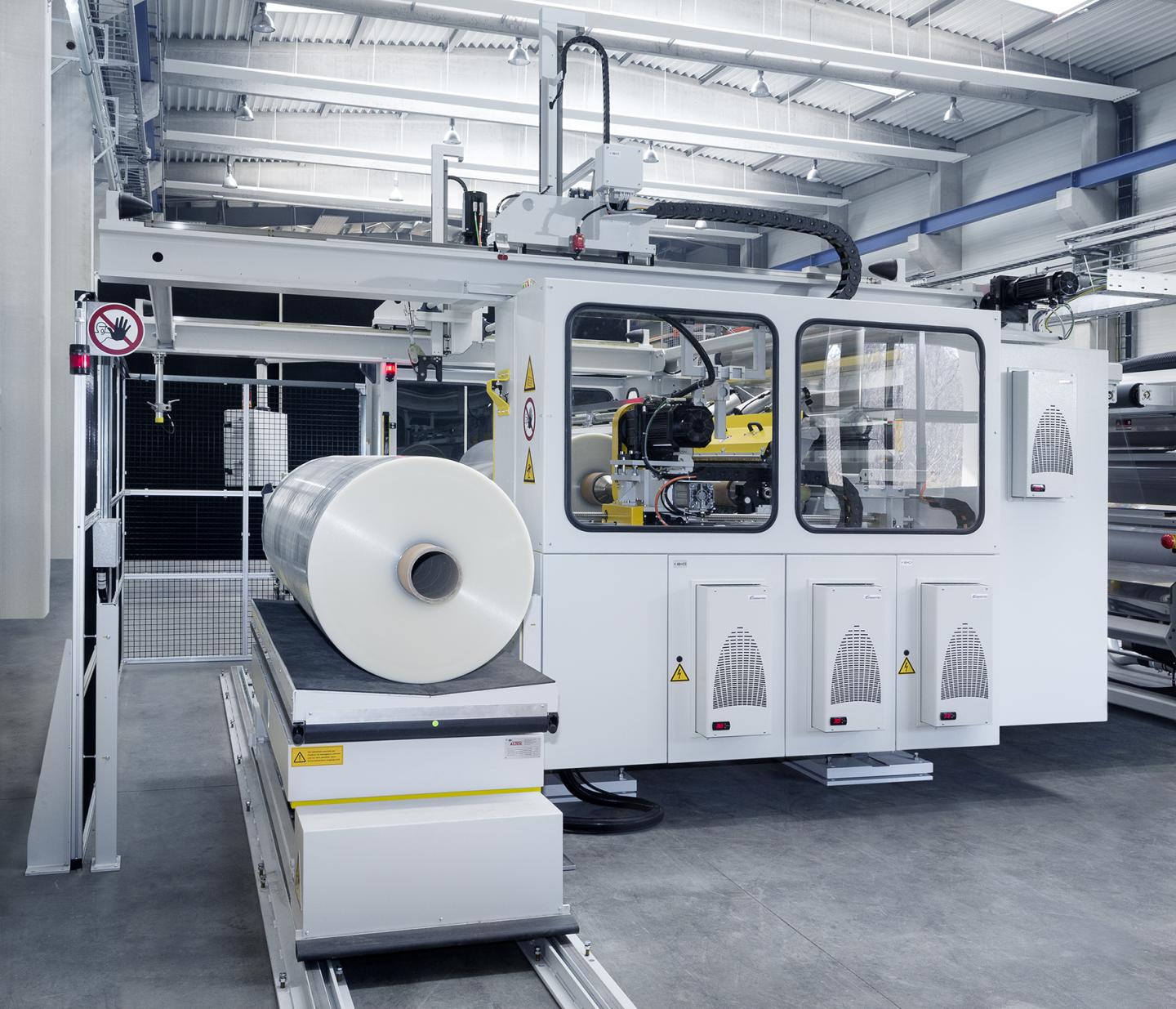
Winding systems
SML has created many different winding systems, which are focused precisely on the demands of film producers and their customers. All of these winders have a solid, vibration-dampening steel frame construction, which is able to resist the dynamic forces generated at high production speeds.