High-performance PP sheet lines now equipped to manufacture premium foamed sheet
New types of thermoforming products from foamed sheet are lightweight, microwaveable, cost-effective and fully recyclable. Due to their excellent insulating properties they are a perfect alternative to products made of EPS. SML’s advanced high-performance PP sheet lines are an optimum solution for the manufacturing of foamed sheet from PP in higher volumes.
EU regulations, such as the single-use plastics directive and the imminent ban on expanded polystyrene (EPS), spell the need for the development of innovative and future-oriented packaging solutions. With this in mind, SML continues to perfect technologies for the production of foamed sheet from PP, especially with regard to food packaging.
Market requirements
“In direct response to customer requirements, we have optimised and upgraded specific components of our high-performance PP sheet lines for the manufacturing of high volumes of premium foamed sheet. Of course, we did this without compromising the lines’ high efficiency and product quality with regard to classic PP thermoforming sheet”, Martin Kastner, R&D Engineer at SML, explains.
40 % material savings with foamed PP sheet
When it comes to SML’s high-performance PP-sheet lines, the total density of PP foamed sheet, which can be achieved, is as low as 0.55 g/cm³, referring to a sheet made from standard polymers with an A/B/A structure, consisting of 20 % conventional PP in the outer A-layers and of 80 % foamed PP in the inner core layer (B layer). Compared with regular PP sheet, this corresponds to a reduction of 40 %. “The lower material input results in significant savings for sheet manufacturers and in lighter packaging,” Martin Kastner explains.
Quality features of foamed PP sheet:
- Excellent heat insulation. The microcells the foam have an insulating effect, which keeps food warm for longer.
The finer the cell structure, the better the thermal insulation. - Microwaveable. Food can be reheated in the tray in accordance with food safety standards.
- Fully recyclable mono-material
- Fat and oil-resistant. For a wide range of different food and non-food applications.
- Excellent mechanical properties. A high stiffness and dimensional stability, thermoformable on conventional thermoforming systems.
High-performance extrusion system
SML’s high-performance PP sheet line is equipped with a coextrusion system that comes with a powerful 180/33 single-screw extruder as the main extruder on which the foamed B-layer can be manufactured. It achieves a plasticising capacity of up to 1,250 kg/h with a mixture of virgin PP and up to 80 % regrind. An HSE 75/37V semi-high-speed extruder serves as the co-extruder (for the A-layers). The complete extrusion system of the line delivers a maximum plasticising capacity of up to 1,850 kg/h.
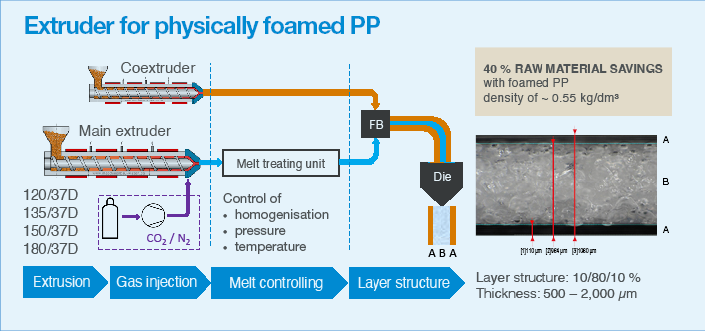
Foaming technology package – customised for PP
For the production of foamed PP sheet, the screw of the main-extruder was given a special design. Furthermore, the extrusion system is fitted with a foaming technology package customised for PP in the melt pipes of the main extruder. The addition of small quantities of inert gases such as C02 or N2 and a nucleating agent into the melt enables the creation of huge quantities of fine microcells in the corelayer (B-layer) of the A/B/A sheet.
Market-proven roll stack technology
The roll stack is a key element in any sheet line. On its high-performance PP sheet lines, SML’s advanced roll stack technology is adapted 100 % to the processing of conventional and foamed PP.
- Smart Parallel Gap (SPG) roller technology for perfect thickness profiles. Quick changes of sheet thickness with minimal die adjustment.
- Thin shell roller. Superior heat transfer coupled with a greater cooling capacity, resulting in a higher specific output.
- Quattro gap. Four roller gaps for better cooling and optimum surface properties, especially for thick sheets.
Due to the special material properties, thermoforming companies are starting to discover the full potential of foamed sheet for future-oriented packaging solutions. SML has been involved in the development of corresponding technologies for years, and meanwhile several lines for foamed sheet are in operation at customer sites.
Redlham, 07.01.2025